State-of-the-art technology in plastic extrusion for innovative industries
State-of-the-art technology in plastic extrusion for innovative industries
Blog Article
A Comprehensive Guide to the Refine and Advantages of Plastic Extrusion
In the large world of production, plastic extrusion arises as a vital and very efficient process. Transmuting raw plastic right into continual accounts, it provides to a variety of sectors with its remarkable adaptability.
Understanding the Basics of Plastic Extrusion
While it may appear complicated at very first glimpse, the process of plastic extrusion is fundamentally straightforward. The process starts with the feeding of plastic material, in the form of powders, pellets, or granules, into a heated barrel. The shaped plastic is after that cooled down, solidified, and cut right into preferred lengths, finishing the process.
The Technical Process of Plastic Extrusion Explained
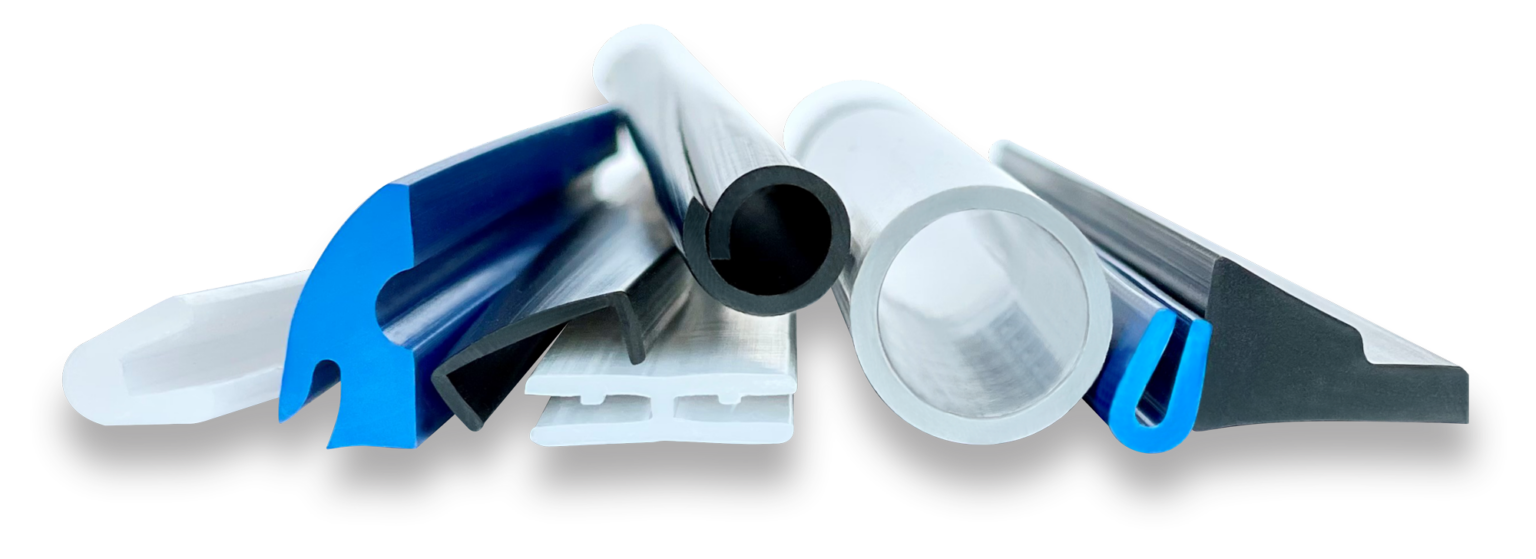
Types of Plastic Suitable for Extrusion
The choice of the ideal kind of plastic is an essential facet of the extrusion procedure. Various plastics offer special residential properties, making them extra suited to particular applications. Polyethylene, for example, is typically utilized because of its affordable and very easy formability. It supplies superb resistance to chemicals and dampness, making it ideal for products like tubes and containers. Similarly, polypropylene is another preferred choice as a result of its high melting factor and resistance to exhaustion. For more durable applications, polystyrene and PVC (polyvinyl chloride) are commonly selected for their toughness and durability. These are typical alternatives, the option eventually depends on the particular requirements of the item being created. Comprehending these plastic types can considerably enhance the extrusion procedure.
Comparing Plastic Extrusion to Other Plastic Forming Methods
Comprehending the kinds of plastic suitable for extrusion paves the way for a wider discussion on exactly how plastic extrusion stacks up against other plastic forming methods. Plastic extrusion is unequaled when read the article it comes to developing continual accounts, such as gaskets, pipes, and seals. It also allows for a consistent cross-section along the size of the item.
Trick Benefits of Plastic Extrusion in Production
In the realm of manufacturing, plastic extrusion offers several considerable benefits. One noteworthy advantage is the cost-effectiveness of the procedure, that makes it a financially attractive manufacturing technique. Furthermore, this method offers superior item adaptability and enhanced manufacturing rate, consequently boosting overall manufacturing performance.
Cost-efficient Production Approach
Plastic extrusion jumps to the forefront as an affordable manufacturing approach in production. In addition, plastic extrusion calls for much less power than typical manufacturing methods, contributing to lower operational prices. On the whole, the financial advantages make plastic extrusion an extremely eye-catching choice in the manufacturing market.
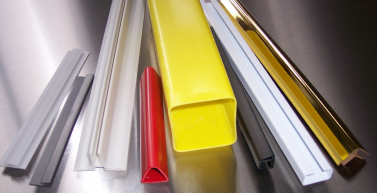
Superior Product Adaptability
Beyond the cost-effectiveness of plastic extrusion, one more considerable advantage in manufacturing hinge on its premium item versatility. This process enables the production of a vast array of items with differing shapes, dimensions, and styles, from straightforward plastic sheets to detailed accounts. The flexibility is credited to the extrusion die, which can be tailored to generate the preferred product style. This makes plastic extrusion an excellent option for industries that call for customized plastic parts, such as automobile, construction, and product packaging. The ability to generate diverse items is not only helpful in meeting details market demands but likewise in enabling makers to explore brand-new product with very little capital investment. Essentially, plastic extrusion's product adaptability promotes advancement while improving functional efficiency.
Boosted Manufacturing Speed
A significant advantage of plastic extrusion exists in its improved production rate. Few other production procedures can match the rate of plastic extrusion. Furthermore, the ability to maintain regular high-speed manufacturing without compromising product high quality sets plastic extrusion apart from other approaches.
Real-world Applications and Effects of Plastic Extrusion
In the world of manufacturing, the method of plastic extrusion holds profound importance. This process is extensively made use of in the manufacturing of a variety of products, such as plastic tubes, window Continue structures, and climate stripping. As an outcome, it greatly affects markets like construction, product packaging, and vehicle markets. Its impact Check Out Your URL expands to daily things, from plastic bags to toothbrushes and non reusable cutlery. The economic benefit of plastic extrusion, primarily its cost-efficient and high-volume result, has reinvented manufacturing. Nevertheless, the ecological impact of plastic waste stays a problem. For that reason, the sector is constantly pursuing advancements in recyclable and biodegradable products, indicating a future where the benefits of plastic extrusion can be kept without endangering ecological sustainability.
Final thought
In final thought, plastic extrusion is a extremely reliable and efficient approach of transforming basic materials right into diverse items. It uses various advantages over various other plastic forming methods, including cost-effectiveness, high output, very little waste, and style flexibility. Its impact is exceptionally felt in numerous markets such as building, automotive, and durable goods, making it an essential process in today's production landscape.
Digging deeper right into the technical process of plastic extrusion, it starts with the selection of the ideal plastic product. Once cooled down, the plastic is cut right into the needed lengths or wound onto reels if the item is a plastic movie or sheet - plastic extrusion. Contrasting Plastic Extrusion to Other Plastic Forming Approaches
Recognizing the types of plastic ideal for extrusion paves the means for a wider discussion on exactly how plastic extrusion stacks up versus other plastic forming approaches. Couple of other production processes can match the rate of plastic extrusion.
Report this page